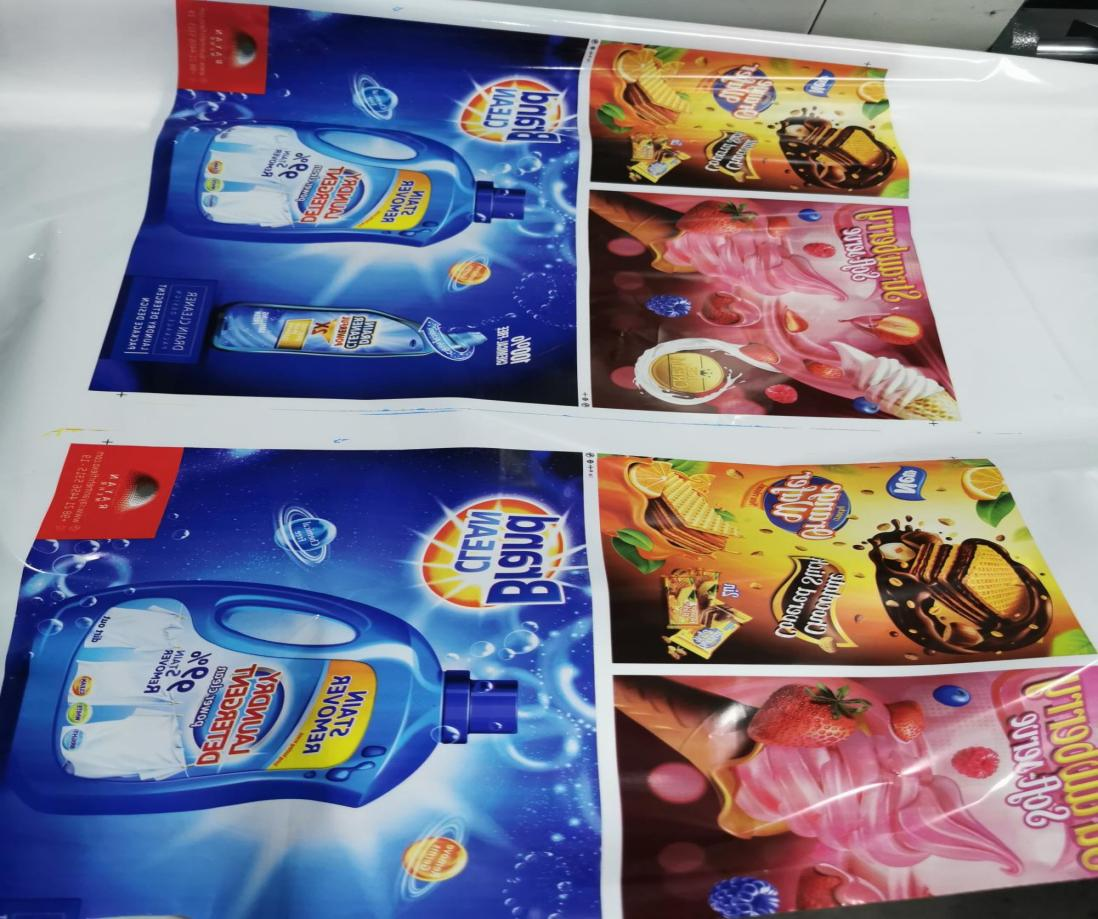
Flexographic printing is a widely used technique in the packaging industry, but achieving consistent and high-quality print results can be challenging. Issues such as poor ink adhesion, uneven color, or blurred images often arise due to a combination of factors, including ink quality, anilox roll specifications, plate design, and operator practices. Below, we explore these factors and provide practical solutions to improve print quality.
1. Ink Quality
Ink is a critical component of the printing process, and its quality directly affects the final output. Common ink-related issues include poor color consistency, drying problems, and adhesion failures.
Solutions:
- Choose the Right Ink: Ensure the ink is compatible with the substrate and printing conditions. For example, water-based inks are suitable for porous materials, while UV-curable inks work better on non-porous surfaces.
- Check Ink Viscosity: Improper viscosity can lead to uneven ink transfer. Use a viscometer to measure and adjust the ink viscosity according to the manufacturer’s recommendations.
- Monitor Ink Drying: If the ink dries too slowly or too quickly, it can cause smudging or poor adhesion. Adjust the drying settings (e.g., temperature, airflow) or consider using additives to optimize drying time.
2. Anilox Roll Specifications
The anilox roll is responsible for transferring ink to the printing plate. Its line screen (measured in lines per inch, or LPI) and volume (measured in billion cubic microns, or BCM) play a crucial role in ink delivery.
Solutions:
- Match the Anilox Roll to the Job: Use a higher LPI anilox roll for fine details and a lower LPI for solid areas. For example, a 600 LPI roll is ideal for detailed graphics, while a 300 LPI roll is better for large solid areas.
- Check Anilox Roll Condition: Over time, anilox rolls can wear out or become clogged with dried ink. Regularly clean and inspect the rolls, and replace them if necessary.
- Optimize Ink Volume: Ensure the anilox roll’s volume matches the ink requirements of the design. Too much ink can cause bleeding, while too little can result in weak color.
3. Plate Design and Quality
The printing plate is another critical factor that affects print quality. Issues such as dot gain, uneven pressure, or plate wear can lead to poor results.
Solutions:
- Use High-Quality Plates: Invest in plates made from durable materials that can withstand repeated use and provide consistent performance.
- Optimize Plate Hardness: Softer plates are better for rough substrates, while harder plates are suitable for smooth surfaces. Choose the appropriate hardness based on the substrate.
- Check Plate Mounting: Ensure the plate is mounted evenly and securely to avoid uneven pressure, which can cause variations in print quality.
- Minimize Dot Gain: Adjust the plate’s dot shape and size to reduce dot gain, especially in halftone printing.
4. Operator Practices
The skill and habits of the operator play a significant role in achieving consistent print quality. Even with the best equipment and materials, improper handling can lead to issues.
Solutions:
- Training and Education: Regularly train operators on best practices for machine setup, ink management, and troubleshooting.
- Follow Standard Procedures: Establish and enforce standard operating procedures (SOPs) for tasks such as ink mixing, plate mounting, and press setup.
- Monitor Print Quality: Encourage operators to conduct frequent quality checks during the run to identify and address issues early.
- Maintain Cleanliness: Ensure the printing environment is clean and free of dust or debris, which can affect print quality.
5. Substrate Considerations
The material being printed on can also impact the final result. Issues such as poor ink adhesion or uneven surfaces can arise if the substrate is not properly prepared.
Solutions:
- Pre-Treat the Substrate: Use corona treatment or primers to improve ink adhesion on non-porous materials like plastics.
- Check Substrate Uniformity: Ensure the substrate is free of defects such as wrinkles, bubbles, or uneven thickness.
- Adjust Settings for Substrate Type: Modify ink viscosity, drying settings, and pressure based on the substrate’s characteristics.
Conclusion
Achieving optimal print quality in flexographic printing requires a holistic approach that addresses ink quality, anilox roll specifications, plate design, operator practices, and substrate preparation. By systematically evaluating and optimizing each of these factors, you can significantly reduce printing issues and produce consistent, high-quality results. Regular maintenance, operator training, and adherence to best practices are key to long-term success in flexographic printing.
If you need further assistance or specific recommendations, feel free to ask!
No responses yet